WHO WE ARE
Associated Engineering Works is a Company established in April 2007 by Director’s Yogendra Agrawal/Archana Agrawal . We performs a Strong, Consistent, Multi-faceted, Multi-disciplinary Company aiming to achieve International Standards and mark a presence in the Construction Industry.
We are specializing in Cost Management and Control, Quality surveying & Value Engineering.
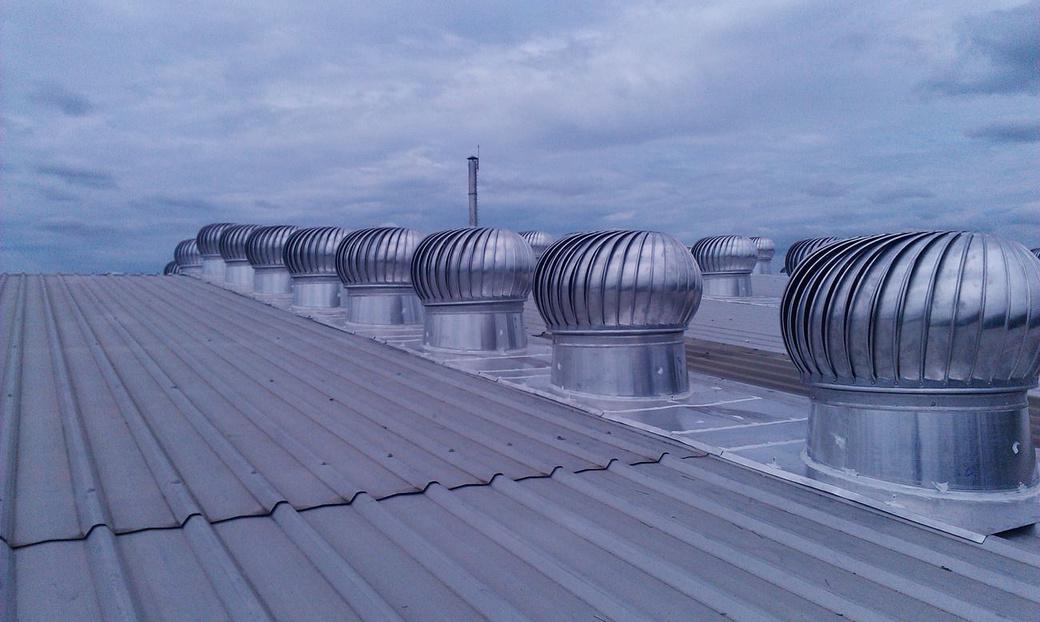
Our Mission & Values
- Enjoys “Challenges”
- Believes In Quality
- Knows the Value of Time & Money
- Possesses the Confidence of Safety
- Possesses High Performance Values
- Maintaining our uncompromising principals and integrity
- Providing building products and services that exceed our customers’ needs and expectations
- Providing environmentally safe products
FRAMING SYSTEM
Designing
Submission of General Arrangement (G.A.) Drawings as per Layout Data Provided by Client for approval.
Approved G.A. comes to Designing phase for preparation of Fabrication Drawings & Sheeting Drawings.
The building is designed in accordance with the following codes:
-As per MBMA.
-Wind load application as per IS 875-Part 3-1987.
-Seismic Load Application as per IS 1893-Part 2 -2002.
PROCUREMENT OF RAW MATERIAL
Galvanized Anchor Bolts (Plate type) having a minimum yield strength of 245
MPa & confirming to IS VSP 2062 (make Sterling or equivalent).
High Strength Bolts shall confirm class 8.8 and above having a minimum Yield
Strength of 830 MPa.
M.S. Bolts confirming grade 8.8 and having minimum yield strength of 400
MPa.
HR Steel Plates having minimum Yield Strength of 345 Mpa for Primary members
(Make SAIL Bhushan, TATA).
Members fabricated by Cold forming process (Purlins, Girt & Rake Angle) shall be Galvanized Sheets and having a minimum yield strength of 345 MPa. (make JSW, or equivalent).
Members Fabricated from Hot rolled structural shapes for Beams & Channels shall confirm to the physical specifications of IS 2062/ 1999 Grade B or equivalent having minimum yield strength of 245 MPa; for Tubes it shall confirm to the physical specifications of IS 4923 or equivalent having minimum yield strength of
345 MPa.
Rod and angle Bracing shall confirm to the physical specifications 2062 of
ASTMA36/1S (or equivalent) and having min. yield strength of 250 MPa.
Roof & Wall Cladding (Bare Galvalume / Color Coated) shall be having min. yield strength of 345 MPa. (make JSW or equivalent).
Gutter, Downtake, Flashing etc. accessories made through PPGI.
Turbo Vents (Alluminium /Stainless Steel) & Polycarbonate for Sky light make
Duratuff.
Insulation (insulation sheet 8 / 12mm) make Aerolam / Divine. Foam Filler for Eave and Ridge.
FABRICATION
The building will be manufactured in accordance with the following codes
-MBMA manual for Fabrication Tolerances.
-AWS D1.1 Structural Welding Code.
Sand Blasting of Steel for removing all foreign material.
Precise metal cutting through state of the arc CNC Plasma Cutting Machine. Members fabricated from Plate shall have flanges and webs Joined on one side of the web by a continuous welding process (SAW) using only ADOR / ESAB electrodes. Continuous inspection of Welding Quality through Dye Penetration Test / Ultrasonic
/ radiographic Testing *(As applicable in terms of Order).
Fabricated member shall be cleaned and given one shop coat (25-30 micron) of Zinc
Chromate, air drying, phenol modified alkyd resin primer/grey primer followed by two coats (50-60 micron) of Gloss Synthetic Enamel (all paints/primer BERGER / ASIAN make).
Roof Sheets / Cladding sheets to be procured directly from manufacturer in desired
Thickness & Length.
TRANSPORTATION
Proper Vehicle Selection as per product to be transported.
Adequate use of Wooden Planks for minimizing damage during transit. Maintaining proper Inter member spacing for facilitation during unloading. Packing the delicate section/members with extra Polythene/Cardboards for minimizing scratches etc.
Limiting Stacking Height as per Members loaded.
Proper Fastening of Members by Shackles/Chains tightened through turn Buckles in open type Transport trailers.
EXECUTION
Regular Visit of Project Engineers at Anchor Bolting Stage to achieve Dimensional accuracy.
Use of Proper and competent Machinery & Operators. (Cranes as per Load Chart). Proper Unloading-Stacking of Material.
Daily basis PPEs Check and Tool Box Talk. Proper Unloading-Stacking of Material.
Use of Competent Lifting Equipments (Loading Belt, Slings, D Shackles, Chain Pulley, Turn Buckle).
Use of Torque Wrench for checking of Adequate Tightening of HT Bolts. Paint touch up for damage occurred during Shifting/Erection.
BENEFITS
Optimized design of steel reducing weight. Easy future expansion/modification.
Voluminous space (up to 30M clear spans, 30 M eave heights). Weather proof.
No fire hazards.
International Quality Standards. Seismic & Wind pressure resistant.
Quality design, manufacturing and erection. Quick delivery and Quick turn-key construction. Architectural versatility.
Energy efficient roof and wall system using Rockwool & PUF insulation. Water-tight roofs & wall coverings.
Pre-painted and has low maintenance requirement. Easy integration of all construction materials. Erection of the building is fast.
The building can be dismantled and relocated easily.
Future extensions can be easily accommodated without much hassle.
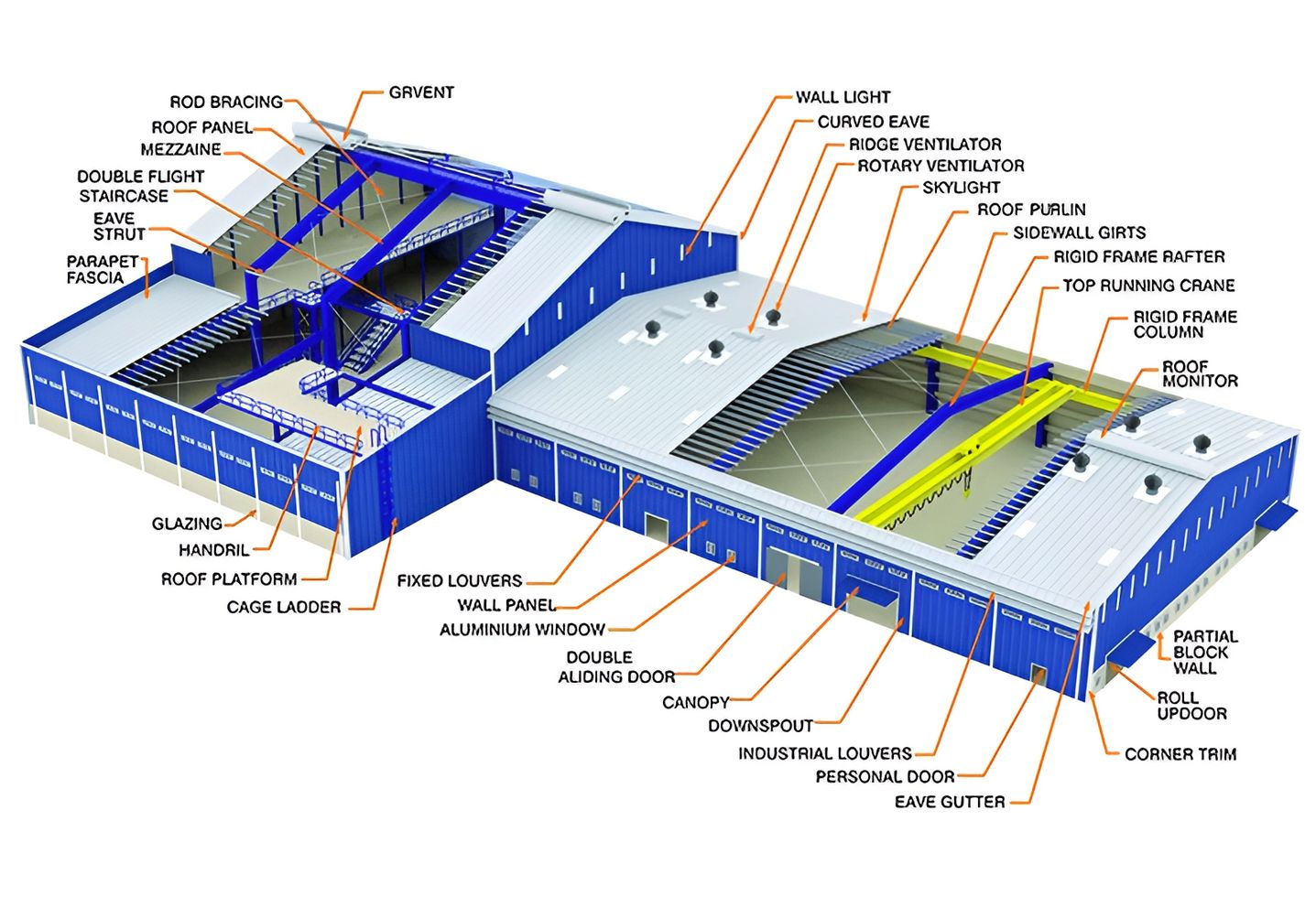
APPLICATIONS
Houses & Living Shelters. Factories.
Warehouses. Sport Halls. Aircraft Hangers. Supermarkets. Workshops.
Distribution Centers. Commercial Showrooms. Labour Camps.
Petrol Pumps/Service Buildings. Schools.
Community Centers. Cold Stores.
Equipment housing/shelters. Telecommunication shelters. “Almost” any low-rise. Restaurants.
Railway Stations.
ABSTRACT
Buildings & houses are one of the oldest construction activities of human beings. The construction technology has advanced since the beginning from primitive consturction technology to the present concept of modern house buildings. The present construction methodology for buildings calls for the best aesthetic look, high quality & fast construction, cost effective & innovative touch. India being a developed country massive house building construction is taking place in various parts of the country. Since 30% of Indian population lives in towns cities hence construction is more in the urban places. The requirement of housing is tremendous but there will always be a shortage of house availability as the present masonry construction technology cannot meet the rising demand every year. Hence one has to think for alternative construction system like pre-engineered steel buildings. India has an installed steel capacity of 35 to 40 million tonnes & apparent steel consumption is around 27 to 30 million tonnes. There is a surplus capacity of flat steel products available in India particularly of hot and cold rolled sheets. These steel components can be utilized in the construction of pre-engineered building components. In preengineered building concept the complete designing is done at the factory and the building components are brought to the site in knock down condition. These components are then fixed / jointed at the site and raised with the help of cranes. The pre-engineered building calls for very fast construction of buildings and with good aesthetic looks and quality construction. Pre-engineered Buildings can be used extensively for construction of industrial and residential buildings. The buildings can be multi storey (4-6 floors). These buildings are suitable to various environmental hazards. PEB Concept has been very successful and well established in North America, Australia and is presently expanding in U.K. and European countries. PEB construction is 30 to 40% faster than masonary construction. PEB buildings provides good insulation effect and would be highly suitable for a tropical country like India. PEB is ideal for construction in remote & hilly areas. The paper drafted covers in detail about the concept of Pre-Engineered Building, its construction system, benefits, applications and pictorial representation of various category of buildings.